Location: Home / News
The transformation and modernization of electromechanical reducers in China's water purification industry
Author: LUKAMAN
Date: 2023-08-01
View: 28
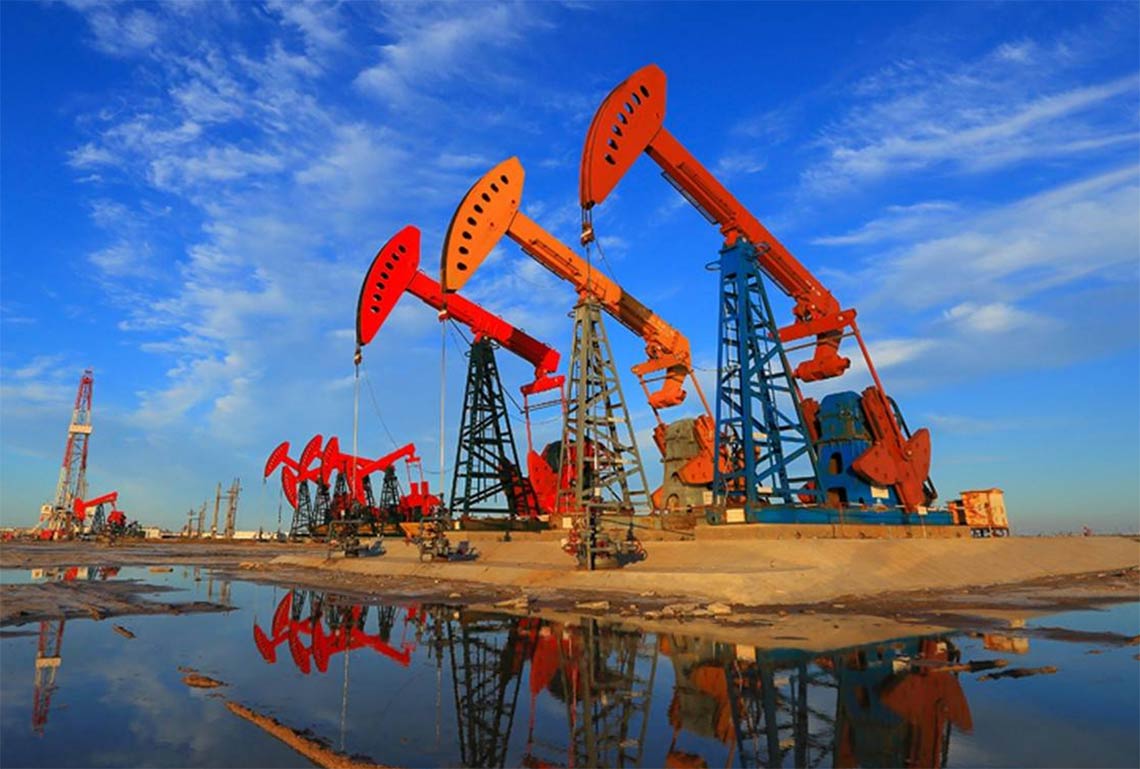
Low energy consumption and efficient treatment of printing and dyeing wastewater have always been topics of continuous research in the industry. In this article, we take a water treatment development company as an example to explain how to achieve low-cost, efficient, stable, and economical wastewater treatment effects through customized solutions. Customize technical solutions with high standards based on application requirements. The project adopts advanced wastewater treatment equipment, and the core technology of the factory adopts A/O treatment technology, greatly improving the urban water environment and playing an important role in pollution control, water quality protection, and natural balance of local catchment areas.
In the process of wastewater treatment, a mixed process is required. It can quickly and evenly mix the added chemical reagents with wastewater, promoting collisions between fine particles and gradually increasing them. Therefore, the condensed particles can be uniformly suspended in the liquid, thereby preventing sedimentation in the flocculation tank. This improves the degree of uniform mixing and ensures good processing results. Due to the 24-hour operation of the sewage treatment plant, wastewater is continuously generated during the operation process and requires timely and effective treatment. If the equipment malfunctions, it may cause downtime and even have a huge impact on the environment. Therefore, the reliability and failure rate of printing and dyeing wastewater treatment equipment are very strict, even if the failure rate is zero. Therefore, we not only need to ensure the safety and reliability of the mixer, but also choose components such as reducers very strictly. If the brake motor fails, it will directly affect the mixing process, and in severe cases, it will affect the throughput of the sewage treatment plant, causing irreversible losses. From the perspective of gearbox selection, in order to solve the problem from the source, it is necessary to adjust it and match it with the height of the mixer. Hybrid dedicated reducers help save 50% of energy. In addition to strict requirements for equipment stability and failure rate, the project also faces some special application environments, such as relatively harsh outdoor water treatment conditions that require 24-hour continuous operation. In addition, the axial force of the stirring blade exceeds 7000 N and the torque is 3500 N. This places higher demands on the output shaft and gearbox bearings.
To cope with the above situation, the project uses a tilted gear coaxial reducer to provide 24-hour uninterrupted operation. IE3 is energy-saving and can save energy for users. These reducers are also equipped with reinforced VL shafts and bearings specifically designed for hybrid use, which can withstand significant radial and axial forces under working conditions. At the same time, with the help of professional testing software, compliance can be analyzed and calculated to obtain the safety factor of the shaft and the service life of the bearings, ensuring the safety of the selection. In addition, NORD also provides RD protective covers for the external vertical installation of the gearbox, which have rainproof function. Its overall IP66 protection level and KB condensate vent prevent harsh on-site conditions. The water entering the engine can not only be discharged from the exhaust port, but also maintain normal operation at a temperature of 0-40 degrees Celsius, ensuring the safe and effective continuous operation of the equipment.